How to Prevent Unexpected Shipping Delays: Proven Strategies for Global Businesses
In the high-stakes world of B2B operations, a shipping delay represents more than a simple inconvenience โ itโs a chain reaction that can disrupt entire supply networks, erode trust, and impact bottom lines. Delays often stem from factors like incomplete documentation, severe weather, or global disruptions such as pandemics. However, the overlooked truth is that even minor errors โ like a mislabeled package or a minor customs hiccup โ can snowball into major logistical setbacks, exposing hidden vulnerabilities. Recognizing and addressing these subtler catalysts is essential for businesses to fortify their supply chain resilience and deliver consistent results in an increasingly unpredictable environment.
In this blog post, weโll go over the hidden factors behind shipping delays, explore their often underestimated financial and operational impacts, and provide actionable strategies to minimize disruptions. By recognizing the root causes and leveraging innovative solutions, you can maintain smooth operations, exceed customer expectations, and safeguard your businessโs reputation โ even in the face of sudden challenges.
Common Causes of Shipping Delays
Delays in the shipping process can arise from multiple sources, many of which are outside your direct control. However, being aware of them allows you to plan ahead, reduce the risk of disruptions, and respond more effectively when they do occur.
Global Events
Major global events โ pandemics, geopolitical tensions, natural disasters โ can create widespread delays throughout the shipping industry. For example, during the COVID-19 pandemic, labor shortages at ports, reduced air freight capacities, and new cross-border regulations caused severe disruptions. Similarly, geopolitical tensions like trade wars or embargoes can lead to rerouted shipments and prolonged delivery times, while natural disasters such as hurricanes can halt operations entirely in affected regions.
Customs and Documentation Issues
One of the common causes of shipping delays is incorrect or incomplete paperwork, a factor often underestimated in its complexity and impact. For instance, a minor error such as a mismatched Harmonized System (HS) code on a shipping label can lead to customs rejecting the shipment for re-evaluation, causing days or even weeks of delay. Similarly, missing certificates or inaccurate product descriptions can halt clearance processes, incur fines, or require additional documentation, further extending transit times and additional storage fees (until merchandise is released).
Weather Conditions
Bad weather โ from hurricanes and snowstorms to flooding โ can severely disrupt shipping routes, often creating unpredictable delays. For example, during hurricane season, ports may shut down entirely to ensure safety, delaying thousands of shipments in one region. Similarly, heavy snowfall can block critical highways, stranding trucks and leaving businesses scrambling for alternative routes. Even under normal conditions, vessels can experience delays due to rough seas, impacting timelines across the supply chain.
Peak Seasons
Peak shipping seasons โ such as the holiday rush in Q4 โ see carriers stretched to capacity, often resulting in longer transit times, backlogs, and higher shipping rates. What many donโt realize is that this strain isnโt limited to the holiday rush; seasonal agricultural exports or end-of-financial-year inventory clearances can also overload logistics networks. For instance, during harvest seasons, the demand for refrigerated containers surges, leaving limited capacity for other goods. Anticipating these niche seasonal demands and diversifying shipping methods can help businesses stay ahead of such lesser-known bottlenecks.
Labor Shortages
Strikes, insufficient manpower at ports, or truck driver shortages can also cause shipping delays, often creating ripple effects throughout the supply chain. For instance, a port strike in a major hub can halt operations, forcing shipments to reroute through less efficient pathways, adding time and cost. Additionally, truck driver shortages in key logistics regions may lead to bottlenecks in overland transportation, delaying goods even after theyโve cleared customs. These labor-related disruptions frequently occur without warning, making proactive workforce planning and partnerships with flexible logistics providers essential for mitigating their impact.
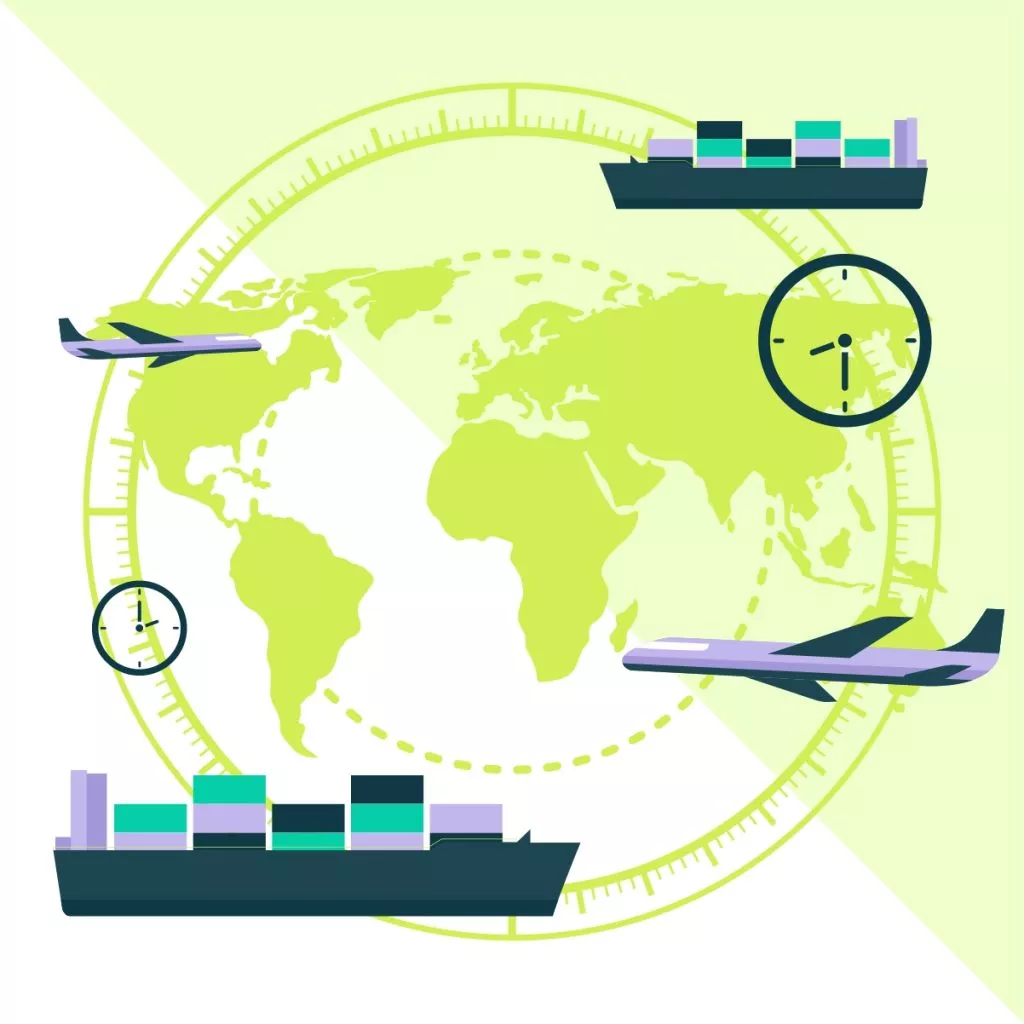
The Impact of Shipping Delays
Shipping delays donโt just irritate customers; they can disrupt entire supply chains and strain B2B relationships, affecting both bottom lines and operational workflows. Beyond the immediate frustrations, late deliveries can jeopardize long-term contracts, erode trust with key partners, and delay production timelines โ a risk no global trader can afford to ignore. Hereโs a quick look at how this impacts businesses:
- Customer Dissatisfaction โ Todayโs customers expect fast, on-time delivery, and delays can do more than just inconvenience them. Beyond complaints and negative reviews, chronic delays erode trust, making B2B buyers hesitant to commit to repeat orders. In sectors like manufacturing or retail, where businesses depend on just-in-time inventory, a single delayed shipment can disrupt production cycles, force emergency procurement, or lead to penalty clauses in contracts.
- Revenue Losses โ Each day a shipment is delayed can lead to canceled orders or missed sales opportunities, contributing to reduced repeat purchases. Additionally, persistent delays may force businesses to incur unexpected costs such as expedited shipping or discounts offered to appease frustrated clients.
- Operational Issues โ When inventory doesnโt arrive as scheduled, your entire production or order fulfillment process may stall, creating bottlenecks that can disrupt delivery commitments to clients. For global sellers, such delays often force a cascade of reactive measures, such as rescheduling production cycles, adjusting labor shifts, or reallocating resources, all of which increase operational costs. In industries like automotive or pharmaceuticals, where precision timing is critical, such delays can result in missed market opportunities or regulatory non-compliance.
- Brand Reputation โ Negative reviews and public complaints about delivery delays can severely damage your brand image, especially in the B2B space where trust and reliability are paramount. For instance, a single viral complaint can lead to a domino effect of lost partnerships and diminished credibility among potential clients. Whatโs often overlooked is how these issues can impact the ability to secure future contracts, as procurement teams often review vendor performance and reputation before committing. Additionally, repeated delays can push customers toward competitors, making it critical to address these challenges proactively through transparent communication and dependable logistics solutions.
Strategies to Avoid Shipping Delays
Even though no one can eliminate delays entirely, understanding where you have the most influence โ and where you donโt โ can help you take proactive steps. Hereโs how to structure your approach to minimize disruptions throughout the shipping process.
1. Factors You Can Control
These are the internal processes and decisions you manage directly, from documentation to day-to-day logistics practices.
Maintain Accurate Documentation and Compliance
Thorough paperwork and regulatory compliance are critical for avoiding customs delays. Ensure that commercial invoices, packing lists, and shipping labels are double-checked for accuracy, as even minor errors can result in significant hold-ups. For instance, a shipment missing proper certificates of origin required under a specific trade agreement might face prolonged inspections or additional tariffs, delaying the entire process. Such cases highlight the importance of understanding and adhering to destination-specific documentation requirements to ensure smooth customs clearance.
Staying updated on each destination countryโs compliance requirements is equally vital. Regulations vary widely and can change frequently, especially in international trade.Partnering with 24/7 local teams to fill out and verify shipping documents can reduce the risk of manual errors, streamline processes, and improve overall efficiency.
Optimize Packaging and Labeling
Proper packaging and precise labeling are critical to ensuring your shipments move smoothly through the supply chain. Poorly packed items not only increase the risk of damage during transit but can also slow down inspections, leading to delays, re-shipments, or even refunds.
Equally important is accurate labeling. Clear, scannable barcodes and labels that match shipping documents help prevent sorting errors and rerouting delays.If shipping to Amazon, make sure you are well familiar with the Amazon pallet requirements.
Implement Real-Time Inventory Management
Digitally enhanced systems play an important role in maintaining seamless operations by providing real-time insights into stock levels and demand trends. This proactive approach helps businesses avoid last-minute stockouts or the need for rushed orders, which can disrupt shipping schedules and inflate costs. For example, tracking regional inventory can identify imbalances and facilitate timely transfers between locations, ensuring continuity in supply.
Automatic reordering complements this by leveraging demand forecasting tools to predict when critical products need replenishment. Setting reorder points based on historical data and seasonal trends ensures you maintain optimal inventory levels, preventing unexpected shortages that could jeopardize delivery commitments. Together, these systems streamline inventory management and enhance operational efficiency.
Forecast Demand and Plan Shipments
Effective forecasting and prioritization are essential for streamlining logistics and avoiding delays. By analyzing historical sales data and identifying seasonal trends, businesses can align production, warehousing, and shipping schedules to anticipate high-demand periods and reduce bottlenecks. For instance, planning ahead for end-of-year holiday surges allows for better inventory positioning and resource allocation.
Equally important is the prioritization of urgent deliveries. Identifying time-sensitive shipments and addressing them first ensures critical goods reach their destination on time. Leveraging backup carriers or having expedited options in place can mitigate the impact of unexpected disruptions, helping maintain service reliability and client trust.
Streamline Internal Communication
Ensuring team alignment is critical for maintaining an efficient supply chain. All departments โ procurement, logistics, and customer service โ must share real-time information about incoming orders, shipping schedules, and potential delays. This transparency ensures that everyone is on the same page, minimizing miscommunication and enabling quicker responses to any disruptions.
Equally important is the establishment of clear standard operating procedures (SOPs) for tasks such as packing, labeling, and handing off shipments. Consistency in these processes reduces human error and ensures that shipments are prepared and documented correctly every time, contributing to smoother operations and fewer delays.
Factors You Have Less Control Over
These are aspects of shipping where external parties or infrastructure are involved, but you can still influence outcomes by making strategic choices and building buffer zones into your operations.
Select Reliable Carriers and Logistics Partners
When selecting carriers and freight forwarders, it is essential to evaluate their performance metrics, including on-time delivery rates, coverage areas, and customer reviews. This thorough analysis provides insight into their reliability and operational capabilities. Additionally, negotiating clear Service-Level Agreements (SLAs) ensures that partners commit to specific handling times or priority loads, creating a framework for improved accountability. While SLAs cannot entirely eliminate risks, they establish shared expectations and help mitigate potential disruptions in your logistics operations.
Leverage Advanced Technology
Real-time tracking and predictive analytics are transforming how businesses manage logistics. digitally-enabled platforms provide visibility into your shipmentโs exact location, allowing you to anticipate delays and take corrective actions such as rerouting shipments or notifying customers proactively. Meanwhile, AI-driven predictive analytics enhance this capability by forecasting busy routes, seasonal demand surges, and potential disruptions. By leveraging these tools, businesses can plan smarter, reduce transit times, and maintain customer satisfaction even during challenging conditions.
Diversify Suppliers and Warehousing
Storing products in multiple locations across different regions or countries can significantly reduce transit times and minimize reliance on a single shipping route. This approach not only enhances flexibility but also ensures quicker deliveries to various markets, especially during regional disruptions. Similarly, diversifying your supplier base is critical to mitigating risks associated with production or shipping delays. Relying on a single supplier leaves you vulnerable to their challenges, but having multiple options allows you to pivot seamlessly if one encounters a bottleneck, ensuring consistent supply chain performance.
Build Buffer Time and Safety Stock
Building buffer time into your delivery schedules and maintaining safety stock are essential strategies for minimizing the impact of unforeseen delays. By adding extra days to your promised delivery dates, you create a cushion that accommodates minor hiccups without compromising customer satisfaction. Similarly, holding a reserve of critical products helps businesses absorb unpredictable spikes in demand or temporary supplier issues. Together, these measures ensure smoother operations and enhance reliability, even when unexpected challenges arise.
Maintain Open Communication with Carriers and Customers
Providing regular shipping updates and coordinating effectively with carriers are essential strategies for maintaining transparency and efficiency in logistics. Automatic alerts or tracking links allow customers to stay informed about their shipment status, easing frustration and building trust, especially in the event of delays. Additionally, sharing volume forecasts and any special requirements with carriers in advance enables them to plan capacity effectively, reducing the likelihood of disruptions and ensuring smoother operations across the supply chain.
Factors You Have Zero Control Over
Some disruptions stem from broader external circumstances โ like global events or natural disasters. You canโt prevent these outright, but you can prepare and respond quickly.
Weather, Natural Disasters, Geopolitical Events
Collaborating with carriers that can quickly pivot to alternative routes during extreme weather or natural disasters ensures that shipments avoid major disruptions when key transport hubs are affected. Additionally, investing in comprehensive cargo insurance mitigates financial risks associated with damaged or delayed shipments due to severe weather conditions. Staying informed about global events, such as pandemics, strikes, or geopolitical tensions, further allows businesses to anticipate potential supply chain disruptions and act proactively. Diversifying manufacturing and shipping routes to more stable regions also strengthens resilience, reducing reliance on vulnerable areas and ensuring smoother logistics.
Regulatory Changes, Customs Protocols, Port Congestion
Monitoring legislative updates and preparing for regulatory changes are critical in mitigating delays. Sudden shifts in tariffs or import/export policies can cause significant holdups if businesses are unprepared. Staying closely connected with legal and compliance teams ensures that necessary adjustments can be made quickly. Additionally, planning for longer lead times to accommodate border checks and evolving customs documentation requirements helps to streamline international shipments. Diversifying port options by maintaining contracts with multiple terminals also reduces dependency on a single route, allowing for flexibility in case of congestion or disruptions. Together, these strategies create a more resilient and adaptable supply chain.
Future Trends in Shipping and Logistics
The steps above focus on current best practices, but the shipping sector continues to evolve. Emerging trends will shape how businesses prepare for โ and avoid โ future delays:
Rise of Automation and AI: Expect more automated warehouses, driverless trucks, and drones to reduce labor-related disruptions. AI-driven analytics will further enhance forecasting, allowing for preemptive rerouting when conditions change.
Growth of Sustainable Shipping Solutions: Many logistics providers are adopting greener fuels and optimizing routes to lower carbon emissions. Environmentally friendly shipping can also deliver cost benefits and improved speeds as providers streamline processes.
Increased Adoption of Near-Shoring: Companies are mitigating far-reaching supply chain risks by moving production closer to their main markets. This shortens lead times and reduces exposure to overseas disruptions.
Interconnected Freight and Logistics Services: All-in-one solutions that link warehousing, freight forwarding, and compliance into a single platform are becoming common. Businesses can manage every step in one ecosystem, making it easier to respond to disruptions.
Conclusion
Shipping delays are a reality of global commerce, but they donโt have to derail your business. By identifying which factors you can control โ such as thorough documentation, precise labeling, and real-time inventory management โ and which ones require contingency planning โ like labor disputes or global events โ you can minimize the frequency and severity of delays.
Staying informed about external factors, choosing reliable partners, leveraging advanced technology, and diversifying both suppliers and routes will go a long way toward keeping your operations fluid. Whether you face a sudden storm, a pandemic, or an unexpected spike in orders, a well-rounded strategy ensures that youโre prepared to handle the challenges and deliver on your customersโ expectations. Need advice and discuss your future shipments? Contact us now, weโre here to help you save!
Frequently Asked Questions (FAQ)
Why are shipping delays so common?
Shipping delays often arise due to a mix of controllable and uncontrollable factors. These can include inaccurate documentation, labor shortages, extreme weather events, and global political or economic disruptions. While some causes are beyond control, addressing issues such as proper documentation and efficient processes can significantly reduce delays.
How can I handle an unexpected delay during a time-sensitive delivery?
In the event of an unexpected delay, prioritize clear and immediate communication with your customers, providing them with an updated delivery timeline. Offer solutions such as expedited shipping, partial refunds, or alternative arrangements where feasible. Explore alternative routes or carriers to minimize disruption, and maintain consistent updates to reassure customers about the progress of their delivery.
What steps can businesses take to avoid shipping delays?
Businesses can proactively reduce the risk of delays by ensuring thorough and accurate documentation. Leveraging technology for real-time tracking and predictive analytics helps identify potential issues before they escalate. Diversifying suppliers, warehouses, and carriers can provide flexibility during localized disruptions. Finally, maintaining transparency with customers and logistics partners fosters trust and smoother operations.
How does choosing the right logistics provider help reduce delays?
Partnering with a reliable logistics provider can make a significant difference in minimizing delays. Reputable providers offer efficient booking processes, extensive carrier networks, advanced tracking technologies, and streamlined customs procedures. Their expertise and infrastructure help address challenges that might otherwise be difficult for a business to manage alone.